Die Lösung
Hier wird die Gesamtlösung und Herangehensweise der Entwicklung und Konstruktion einer autarken Spannvorrichtung für WFG-Ringe (Warmformgebungsringe) in einzelnen Schritten und anhand von Bildmaterial erklärt.
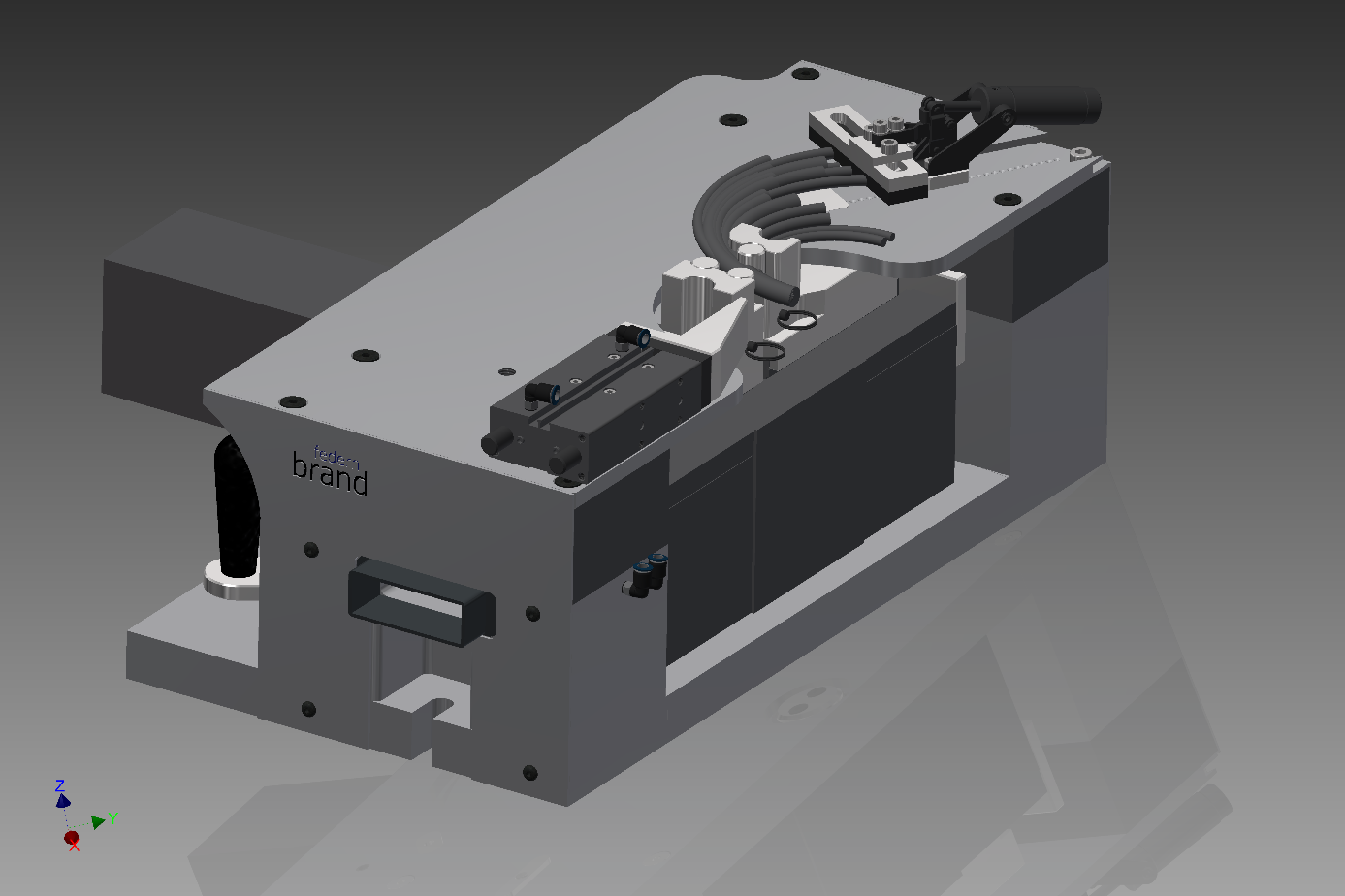
Bild 1-1: Gesamtkonstruktion
Die zerspanende Bearbeitung wird durch eine CNC-Fräsmaschine mit waagerecht verlaufendem Spindelantrieb und einem 30°-45° modularem Fasenfräser realisiert. Zu Beginn werden durch Anwendung des Brainstormings verschiedene Gedanken und Lösungsvarianten zusammengetragen. Aus diesen Vorschlägen und möglichen Lösungen ergibt sich, das Spannen mit einem Zentrumspanner über drei Punkte umzusetzen. In Absprache mit Federn Brand wird die Verwendung eines vorhandenen Zentrierspannstocks PZ100 als Basiselement der Vorrichtung festgelegt. Hierdurch ergibt sich die Möglichkeit, ohne großen Kostenaufwand, erste Spannversuche durchzuführen. Für diese Versuche werden Spannbacken mit passender Aufnahme für den vorhandenen Zentrierspannstock konstruiert. Um das Spannen über drei Punkte und die Abdeckung der großen Variantenvielfalt, ohne den Einsatz von Formteilen zu ermöglichen, wird der Einsatz von Zylinderstiften vorgesehen. Dadurch ergibt sich die Anforderung, eine geeignete Aufnahme in die Konstruktion der Backen einzubringen. Diese wird mit Passbohrungen an den Spannflächen, welche in einer Dreipunktanordnung eingebracht werden, verwirklicht (siehe Bild 1-2). Als zusätzliche Unterstützung der sicheren Spannung und zur automatischen Höhenzentrierung, werden in die Zylinderstifte umlaufende Prismen eingebracht. Es werden zwei Varianten vorgesehen, welche eine Einteilung der Drahtdurchmesser von 3-8mm und 8-13mm besitzen und somit eine bessere Aufnahme der WFG-Ringe ermöglichen. Die eingeschliffenen Prismen besitzen einen Öffnungswinkel von 130° und unterscheiden sich lediglich in der Tiefe des Anschliffs (1,19mm und 3,29mm). Ein Austausch und gleichzeitiger fester Sitz der Zylinderstifte in den Spielpassungen wird über einen radialen Anschliff und eine Sicherung durch Steckbolzen mit Schlüsselring umgesetzt. Nach Abschluss der Konstruktion und Rücksprachen mit dem Projektbetreuer werden die Spannbacken und Zylinderstifte im Werkzeugbau gefertigt.
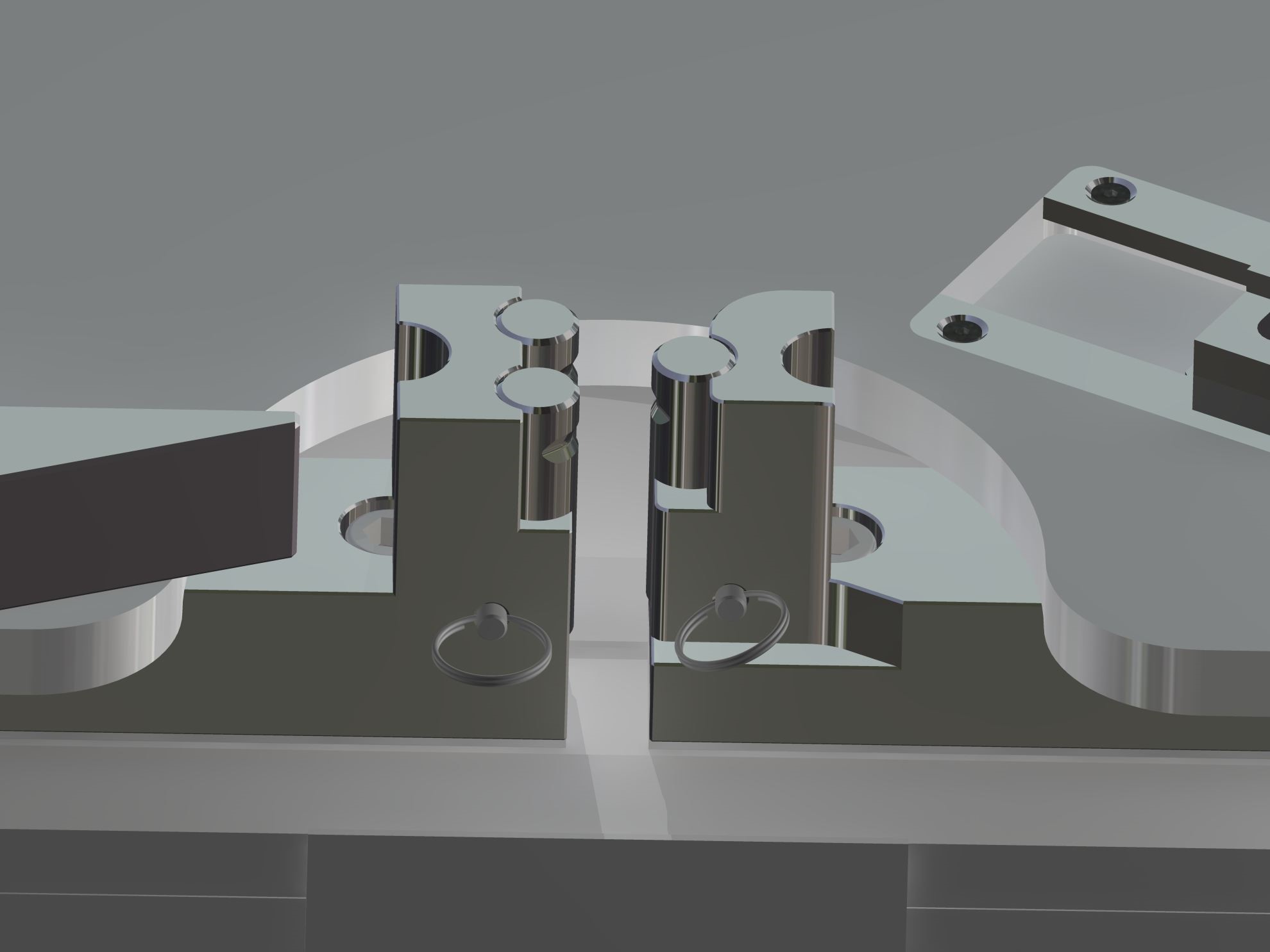
Bild 1-2: Detailansicht Spannbacken
Anschließend wurden Spannversuche durchgeführt, um das Bewegungsverhalten beim Spannen der verschiedenen Ringgeometrien zu erproben. So konnte das Ausmaß der Auflagefläche und der benötigten Verstellmöglichkeiten bestimmt werden. Es ergab sich die Erkenntnis, dass eine Höhenverstellung der Auflagefläche zur Anpassung an die verschiedenen Durchmesser von Nöten ist. Unter anderem muss der Punkt der zu bearbeitenden Fläche gleichbleibend festgelegt werden, um eine Reproduzierbarkeit und eine Verringerung der Rüstzeiten zu ermöglichen. Weiter muss eine Drehung des Zentrierspannstocks von bis zu 45°, zum Ausgleich der Verdrehung der Bearbeitungsfläche, in die Konstruktion eingebracht werden. Da die WFG-Ringe an der zu bearbeitenden Seite relativ kurz gespannt werden, ergibt sich die Anforderung, das hintere Ende zur zusätzlichen Sicherung der Dreipunktspannung mit Hilfe eines Niederhalters auf die Auflagefläche zu pressen.
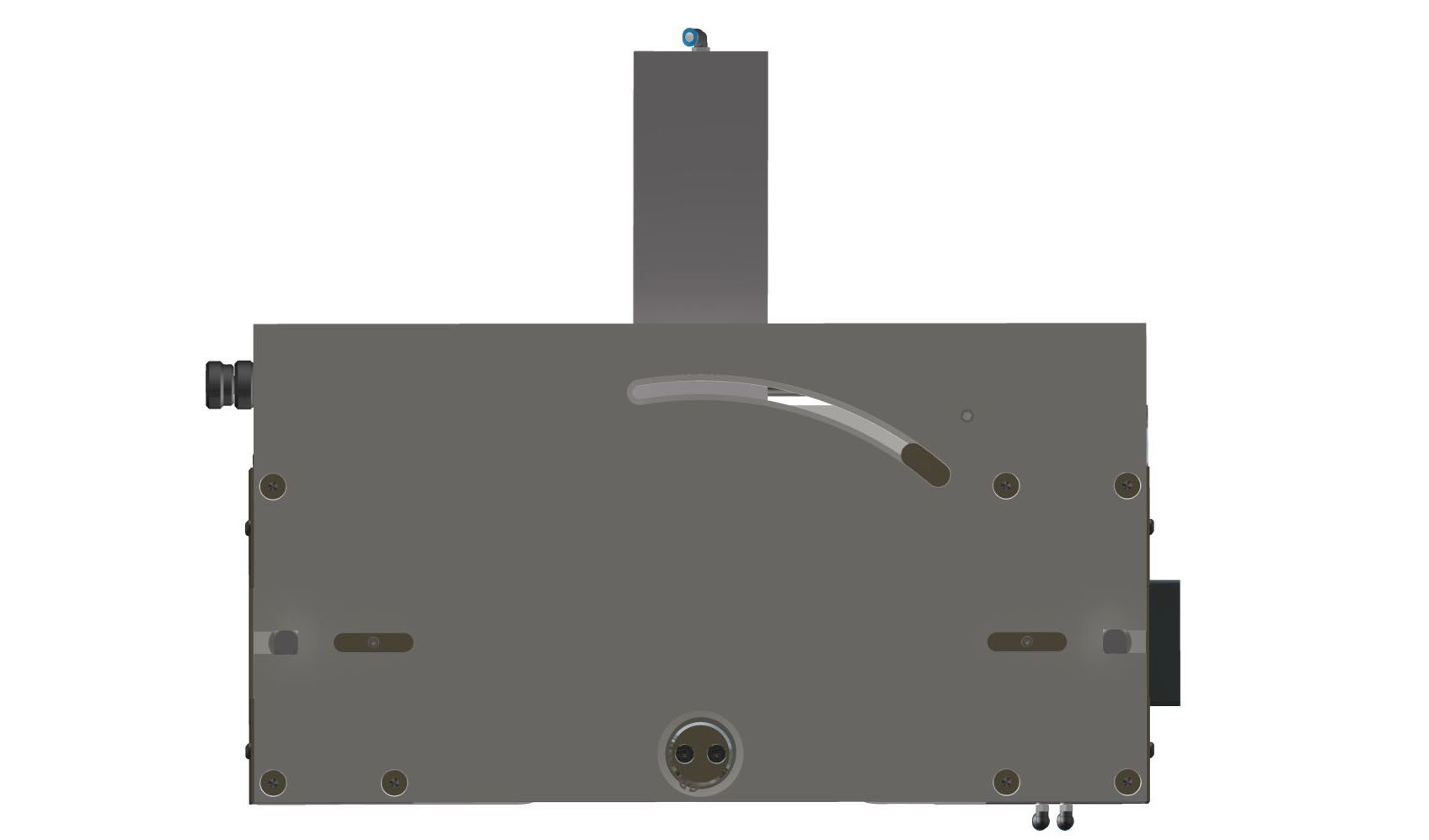
Bild 1-3: Spannvorrichtung von unten
Diese Erkenntnisse bestimmten den weiteren Aufbau der Konstruktion. Als Basiselement der Vorrichtung wird eine Grundplatte erarbeitet (siehe Bild 1-3). Zurerst sind hier die Anbringung von Passfedernuten und Ausfräsungen zur Ausrichtung und Befestigung auf einem Maschinentisch zu erwähnen. Des Weiteren wird eine halbrunde Einfräsung eingebracht. Der Gedanke dabei ist, einen Drehteller einzusetzen, durch welchen ein Verdrehen des Zentrierspannstocks möglich gemacht werden kann (siehe Bild 1-4). Der Mittelpunkt dieser Einfräsung wird so definiert, dass er lotrecht zur Bearbeitungsfläche des gespannten WFG-Rings liegt und gleichzeitig eine Mögichkeit zur Befestigung und Lagerung des Drehtellers darstellt. Die Lagerung erfolgt hierbei durch einen Bolzen, welcher in einer Glycodurbuchse eingesetzt ist und über Bohrungen fest mit dem Drehteller verschraubt ist. Dann wird der Drehteller mit Hilfe des Bolzens und eines Wellensicherungsrings mit der Grundplatte verbunden. Über diesen Drehpunkt wird nun eine Anpassung an die verschiedenen Ringgeometrien und Einhaltung der Parallelität der Bearbeitungsfläche zum Fräswerkzeug ermöglicht.
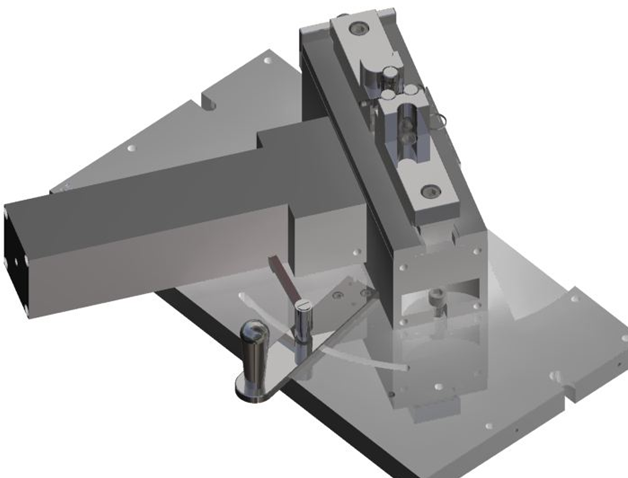
Bild 1-4: Detailansicht Spannvorrichtung verdreht
Um die Einstellmöglichkeit der Drehung zu vereinfachen, wird eine Winkelverstellung vorgesehen (siehe Bild 1-5). Die Verstellung wird fest mit dem Drehteller verschraubt und verstiftet. Sie beinhaltet einen Handgriff, eine Klemmung durch einen handelsüblichen Klemmhebel und einen Radial-Nutenstein, sowie einer kleinen Zentrierung an der Unterseite. Mittels des Klemmhebels und des Nutensteins in Kombinantion mit einer in die Grundplatte eingebrachten Radialnut, erigibt sich eine geführte Verstellmöglichkeit des Winkels, welche gleichzeitig begrenzt werden kann. Bei der Konstruktion ist darauf zu achten, dass auch der Mittelpunkt der Radialnut vom Mittelpunkt des Drehtellers ausgeht. Die Zentrierung an der Unterseite der Winkelverstellung dient als Fixpunkt für einen in der Grundplatte eingesetzten Gewindestift mit Druckkugel. Des Weiteren ist eine Winkelskala zur Vereinfachung der Einstelmöglichkeiten entlang der Radialnut angebracht.
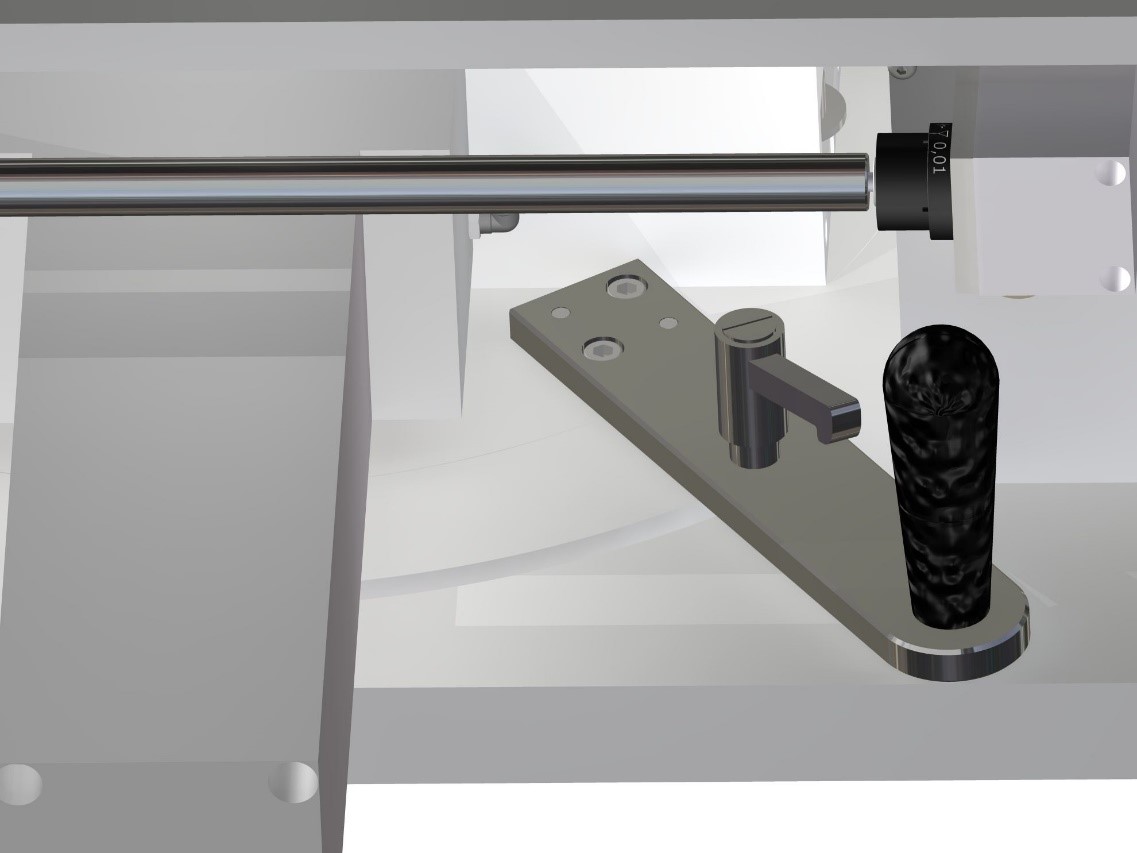
Bild 1-5: Detailansicht Winkelverstellung
Als weitere Anforderung ist eine Höhenverstellung der Deckplatte, zum Ausgleich der Auflagefläche, an die verschiedenen Durchmesser der WFG-Ringe angebracht. Dies wird durch hochpräzise Schwalbenschwanzführungen mit einem Hub von 8mm ermöglicht (siehe Bild 1-6). Sie sind beidseitig neben dem Zentrierspannstock angebracht und mit der Deckplatte verschraubt. Die Verstellung des Hubes erfolgt mit einem Skalenrad. Um eine parallele Höhenanpassung zu gewährleisten sind die beiden Führungen mit Winkelgetrieben ausgestattet und mit Hilfe einer Welle miteinander verbunden. So wird eine gleichmäßige Verstellung von einer Seite realisiert. Da die Bauhöhe der Schwalbenschwanzführungen nicht ausreicht um den Abstand zwischen Grundplatte und Deckplatte zu überbrücken, werden die Schwalbenschwanzführungen auf Abstandshalter aus Aluminiumblöcken gesetzt. Durch diesen Schritt wird eine Anpassung der Auflageplatte an die Ringdurchmesser ermöglicht. Anschließend musste ein Anschlagpunkt für die zu bearbeitende Fläche angebracht werden. Dieser ist zum Erhalt einer reproduzierbaren Positionierung unumgänglich. Aus diesem Grund wird ein DFM-Zylinder auf der Oberseite der Deckplatte angebracht (siehe Bild 1-7). Die Position der planaren Anschlagfläche wird exakt im Mittelpunkt des Drehtellers definiert. In vorderer Endlage gibt der Zylinder nun einen Anschlagpunkt für die zu bearbeitende Stirnfläche der WFG-Ringe vor. Eingefahren gibt der Zylinder den erforderlichen Raum zur zerspanenden Bearbeitung frei.
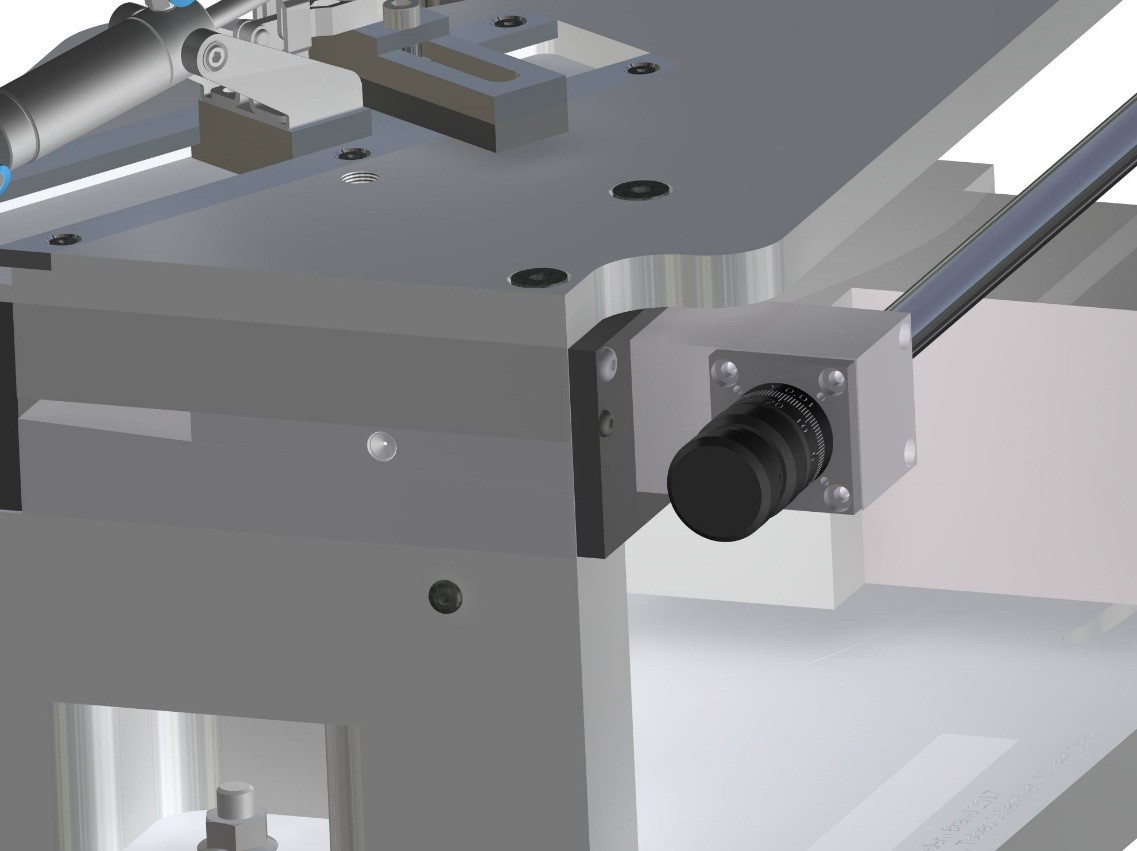
Bild 1-6: Detailansicht Schwalbenschwanzführungen mit Winkelgetriebe
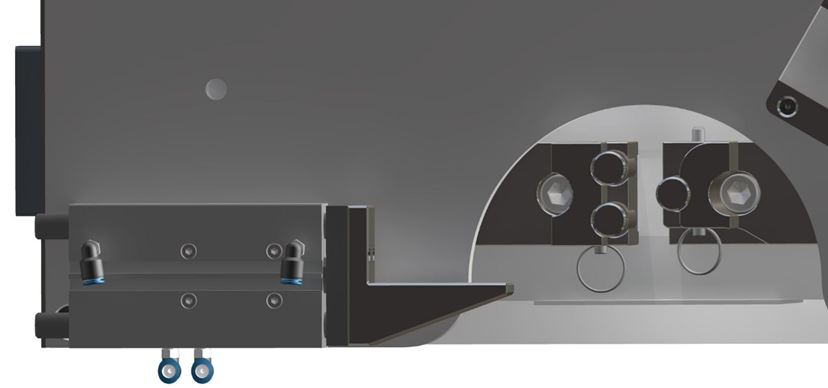
Bild 1-7: Detailansicht Anschlag DFM-Zylinder
Des Weiteren wurde eine Ausfräsung im Bearbeitungsbereich eingebracht, um genügend Freiraum für die Spannbacken, während der Winkelverdrehung des Zentrierspannstocks zu ermöglichen.
Als zusätzliche Unterstützung für ein sicheres Spannen der WFG-Ringe, muss eine Möglichkeit für die Anbringung eines Niederhalters geschaffen werden. Dies erfolgt über eine Nut in der Deckplatte (siehe Bild 1-8). In der Nut lässt sich der Niederhalterspanner verschieben, um den Spannpunkt auf der Auflagefläche an die Ringlängen anpassen zu können. Dies erfolgt mittels zweier Leisten, welche an den Längsseiten der Nut verschraubt sind. So ergibt sich eine T-Nutenführung und die Möglichkeit den Niederhalterspanner auf einem passenden Schlitten fest geführt zu verschieben. Als Rastpunkte sind hier, wie in der Winkelverstellung, kleine Zentrierungen eingebracht. Es dient erneut ein Gewindestift mit Druckkugel, welcher in dem Schlitten verschraubt ist, zur Positionierung in den Zentrierungen. An dem Niederhalter ist zudem eine Platte mit Gummidruckstück vorgesehen. Diese Platte lässt sich über ein Langloch verstellen und dient somit als weitere Anpassungsmöglichkeit an den eingelegten WFG-Ring.
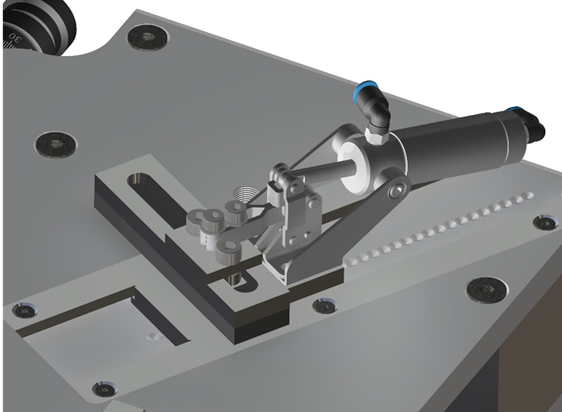
Bild 1-8: Detailansicht Niederhalter in Führungsnut
Um einen sicheren Aufbau während des Rüstvorgangs und das Handling mit einem Kran zu gewährleisten, sind zwei Gewindebohrungen auf der Schwerpunktlinie der gesamten Konstruktion in die Deckplatte eingebracht. Hier können für Transportzwecke Augenschrauben eingeschraubt werden. Der Steuerungs- und Druckluftanschluss wird mittels eines Harting-Steckers ermöglicht. So ergibt sich ein einfacher und unkomplizierter Anschluss an die erforderlichen Versorgungsnetze. Um eine Verlegung der Kabel- und Schlauchanschlüsse möglichst unsichtbar und sicher zu gestalten, wird erneut an der Konstruktion der oben erwähnten Abstandshalter aus Aluminiumblöcken gearbeitet (siehe Bild 1-9). Durch die Baugröße eben dieser ergab sich die Möglichkeit, die Verlegung und den Anschluss des Harting-Steckers in eine gefräste Tasche in dem Abstandshalter platzsparend einzubringen. Ebenfalls wird ein Drucktaster in den Abstandshalter eingelassen. Dieser dient als Starttaster für den Spannvorgang und gleichzeitig als Abfragebestätigung. Sind alle Spannelemente in richtiger Position, leuchtet der Taster grün und gibt dem Bediener somit das Signal, dass die Bearbeitung an der CNC-Fräsmaschine gestartet werden kann.
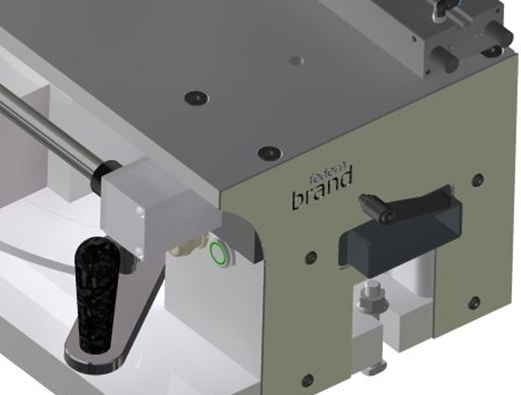
Bild 1-9: Detailansicht Hartingstecker und Starttaster